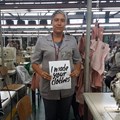
![]() |
K-Way's lean local manufacturing machineSouth Africa's clothing and textile industry has seen some trying times. In the past 15 years, jobs in the local sector have decreased from 200,000 to 19,000 and numerous factories have shut their doors - some following reports of worker exploitation. Then there's the competition from large international retail chains and brands with an eye on increasing their South African footprint, their profits sometimes built on the backs of low-cost foreign labour sourced from the likes of China and Bangladesh. But rising above the challenges is outdoor apparel brand K-Way, which since being founded in Cape Town in 1981, has not only gone on to vastly improve its production efficiency but has also played a part in addressing the country’s unemployment crisis. ![]() The proudly South African manufacturer has its roots in the bespoke tailoring industry; producing made-to-measure uniforms along with customised jackets and foul weather gear for the police force and security industry. The company soon began supplying South African outdoor adventure store, Cape Union Mart, with technical clothing – giving the retailer an edge as this type of apparel was only available from overseas suppliers at the time. Manufacturing efficiencyWhile the business performed reasonably well during its early days, new management appointments in 2004 and the application of a lean manufacturing system spearheaded by Bobby Fairlamb, contributed to a number of improvements in terms of quality, pricing, innovation and delivery. This resulted in a spike in sales growth together with the company pioneering a number of firsts on the African continent. Among these were being the first manufacturer of rain- and storm-proof, seam-sealed, foul weather protective clothing; being the only African company to have been awarded a licence to manufacture clothing using the technical Gore-Tex fabric and more recently, becoming the first African manufacturer to use Sewfree technology in the production of technical clothing. Staff and enterprise developmentK-Way has invested heavily in its workforce, providing staff across the board with ongoing skills training to improve their daily work procedures, methods and systems. This, combined with healthy working conditions and a management team willing to listen to the ideas of employees on all levels has resulted in reduced staff turnover and low absenteeism. The company’s workforce has swelled by 65% and now employs over 240 staff - 50% of them have been with the company for over five years and many hail from the communities surrounding the workshop in Ottery, Cape Town. Furthermore, as part of K-Way’s commitment to local enterprise development, it has nurtured a number of smaller, outsource Cut, Make and Trim (CMT) factories, assisting them with development and training as well as lending them machines. There are now over 150 people permanently employed through these CMTs. ![]() K-Way’s improvement efforts have been well recognised, with the business winning a spate of awards over the past 10 years from the DTI, CCTC and Productivity SA. Other accolades accrued include being named Best Practice Workplace Provider by the Fibre Processing and Manufacturing (FP&M) SETA and taking home Leadership Management International Inc.’s award for Outstanding Achievement. Today, K-Way is the number one supplier to Cape Union Mart and the best-selling brand in South Africa’s outdoor apparel market. Despite this, the company says it is committed to constant improvement and evolution to ensure that it remains on the cutting edge of technology. After a recent tour of the K-Way factory, manufacturing team leader Bobby Fairlamb let us in on how he adapted the lean manufacturing system to the K-Way business, which elements are needed to create award-winning production models and why he believes SA's clothing manufacturing sector has especially large potential to employ people in large numbers.
K-Way has spent much of its time training and developing the staff on the model and its tools that enable the sustainability of continuous improvement. K-Way started with the simple application of waste walks (observation) where all staff are taught to look for waste and eliminate it. Tools that have been successful are problem-solving (A3’s), Kanban and reduction of inventory. It has been quite a simplistic approach to embedding a transformation in the culture.
With K-Way being part of the Cape Union Mart family, it has given impetus to the buying team to actively pursue design, development and production as it is our own manufacturing facility. From K-Way’s perspective we have also actively made a point of offering our retail partner a competitive advantage by being innovative, flexible, punctual (on-time delivery), quality-driven and cost-effective.
For example: • We decide what product to make So, in light of the above, if our businesses are inefficient and uncompetitive it's more likely a management issue rather than a worker or environment issue.
In 2004, the K-Way Factory was struggling, along with the rest of the market. However, when I joined the company, things started to turn around and today it is a flagship model of success and an example of what can be achieved with investment in people and technology being the main drivers.
• A healthy culture which values and respects people and recognises that people are the company’s most valuable asset.
For this to happen it will require that industrialists and entrepreneurs team up with retail and embrace niche products and technology to differentiate themselves from the low-cost run of the mill type products; which, ends up being a race to the bottom in trying to compete with other low-cost businesses locally and abroad. In addition to this, manufacturers need to embrace modern manufacturing techniques and need to explore and use proven management models and systems, such as lean manufacturing. Shop K-Way exclusively at Cape Union Mart and connect with the brand on Facebook, Twitter and Instagram. About Lauren HartzenbergManaging editor and retail editor at Bizcommunity.com. Cape Town apologist. Dog mom. Get in touch: lauren@bizcommunity.com View my profile and articles... |